DEHA:MES
Specialized Manufacturing Management Solution
- A tailor-made MES solution designed to meet the practical needs of each manufacturing enterprise.
- Easily integrates with SCADA and IIoT systems.
- Provides a comprehensive and intuitive view of the entire factory production operations.

Benefits of the DEHA:MES

DEHA:MES is a customized manufacturing execution system (MES) designed to address the specific needs and operational challenges of each enterprise.
This solution is especially suitable for factories with 20 or more machines, and unique operational processes that standard off-the-shelf software cannot effectively support.
Here are four key benefits this solution delivers to your business:

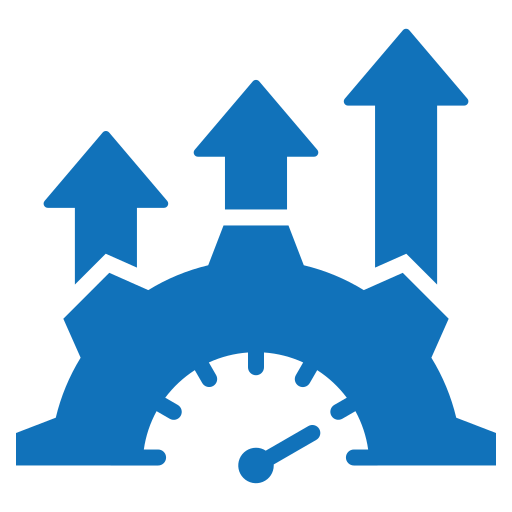
IMPROVED QUALITY
Supports comprehensive quality control across all three stages: IQC, PQC, and OQC, enabling timely detection of product defects and thereby reducing the defect rate.
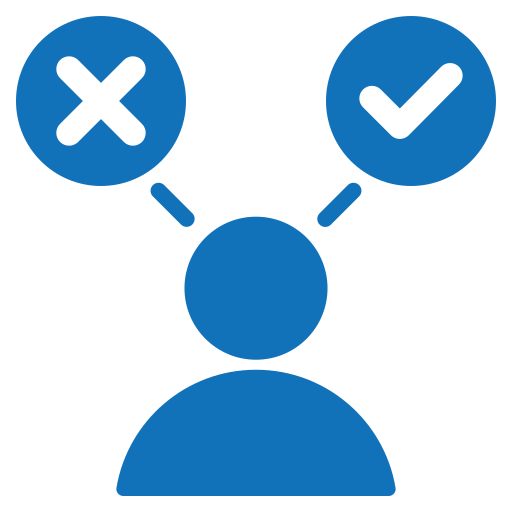
BETTER DECISION MAKING
In-depth analytics from DEHA:MES empower business leaders to make strategic decisions quickly and accurately.
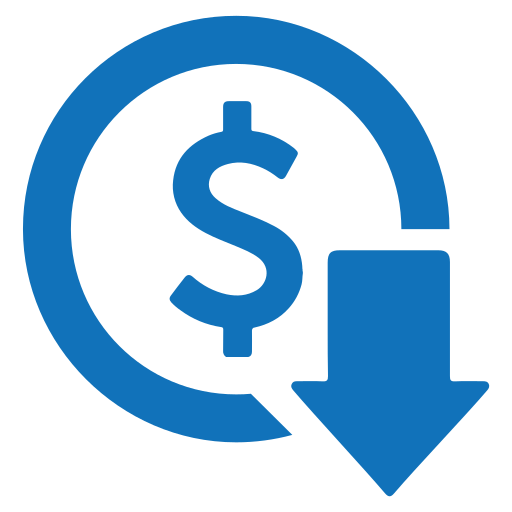
COST SAVINGS
Optimizes procurement processes and raw material usage to minimize transportation and warehousing costs.
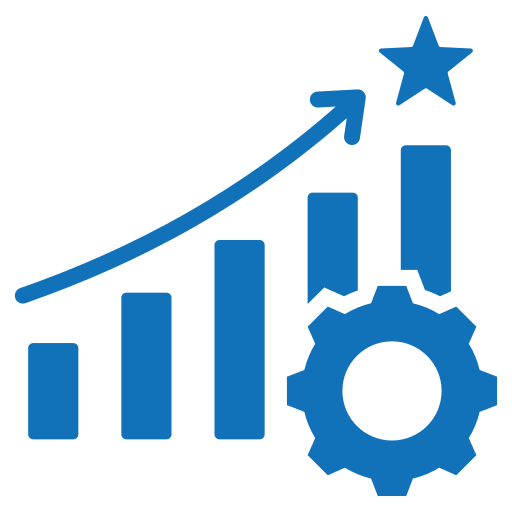
ENHANCED PRODUCTIVITY
DEHA:MES streamlines production processes, minimizes machine downtime, and reduces material waste.
DEHA:MES fits a wide range of manufacturing industries

Many manufacturing sectors have unique operational processes that require highly customizable management systems tailored to their specific needs. DEHA:ERP is designed to address management challenges across various industries. Below are some of the manufacturing industries where DEHA:ERP can effectively solve critical management issues.
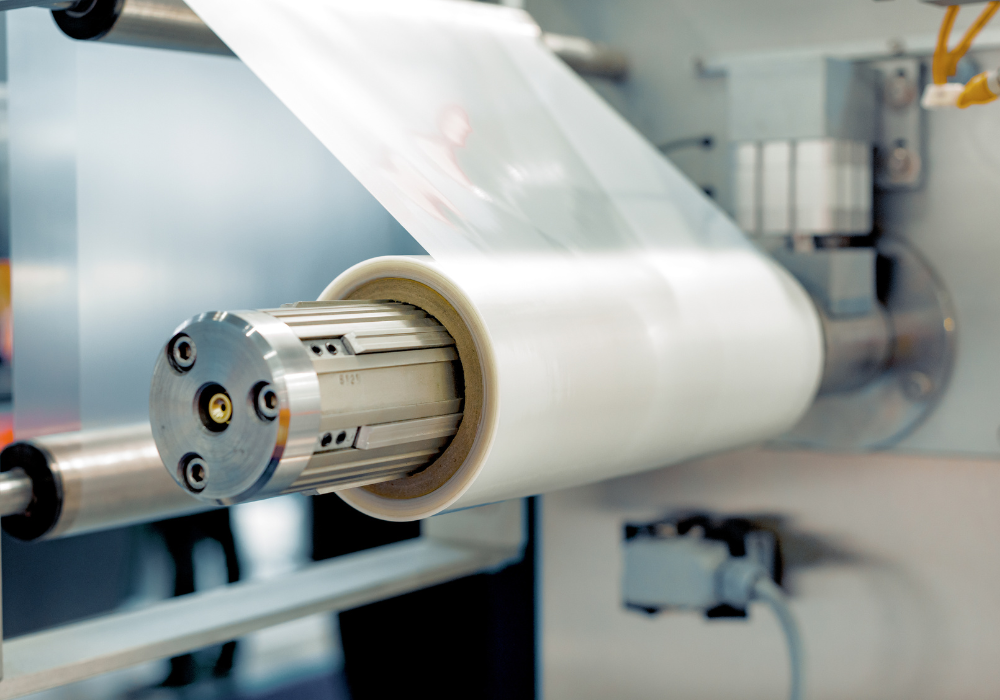
Packaging & Labels
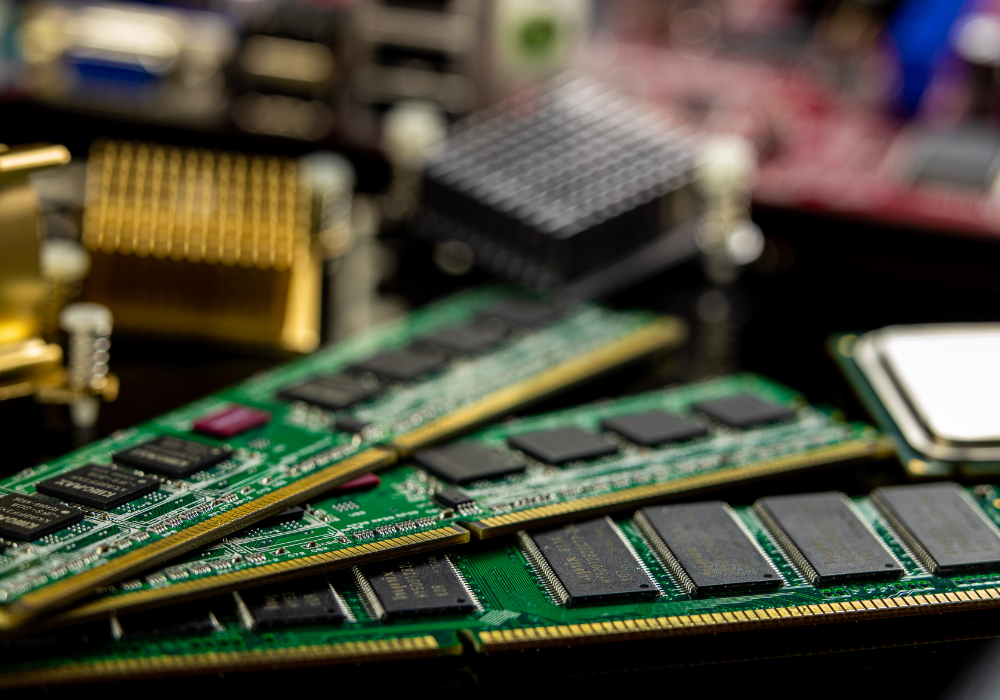
Electronic Components
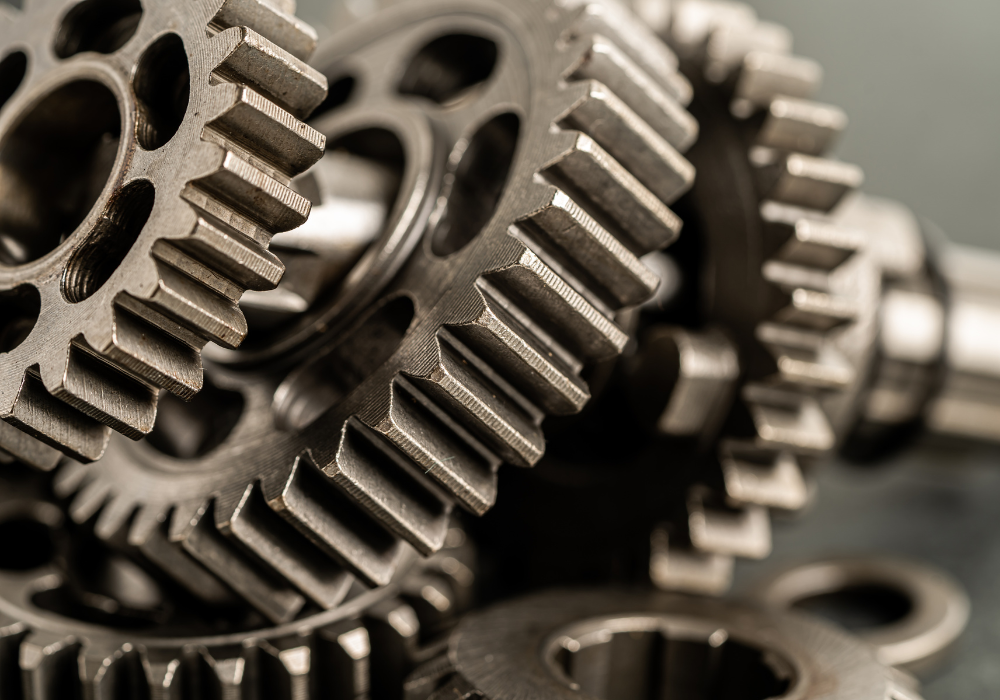
Mechanical Engineering
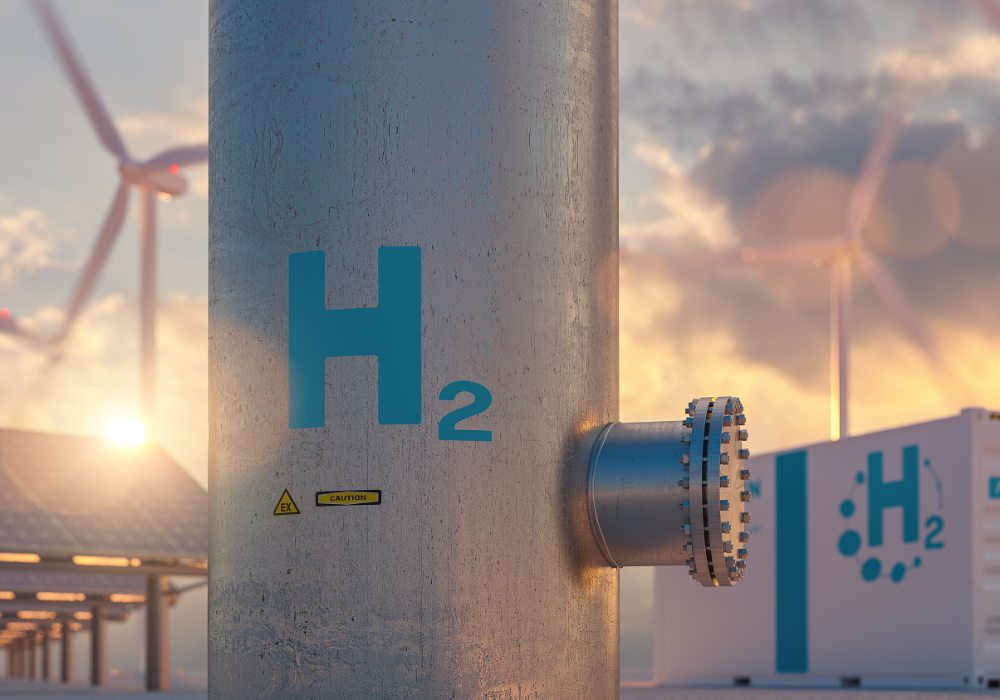
Energy
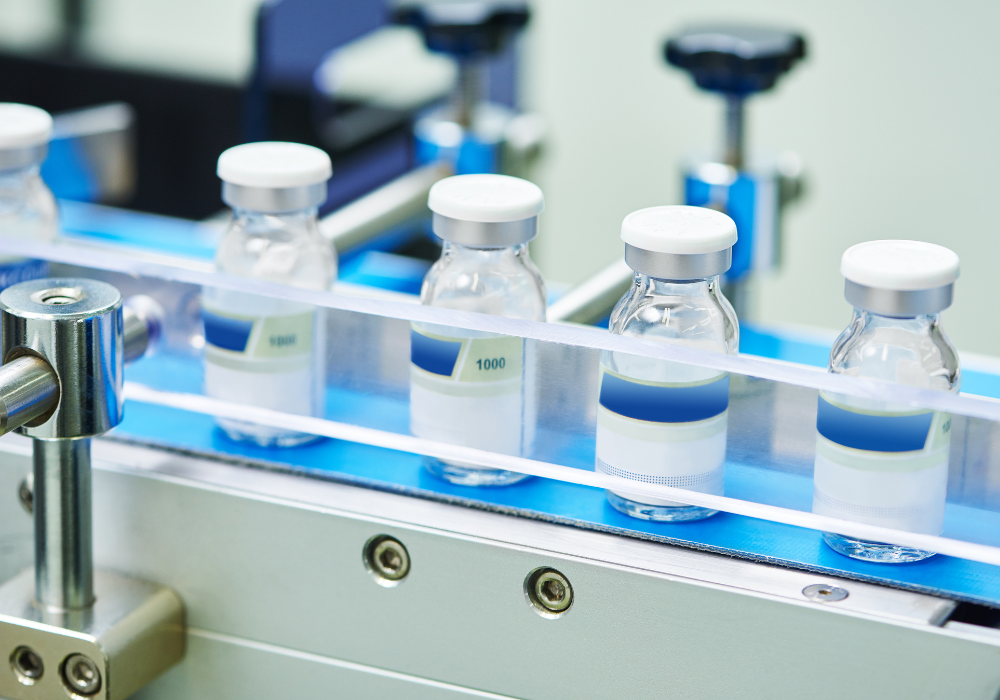
Pharmaceuticals
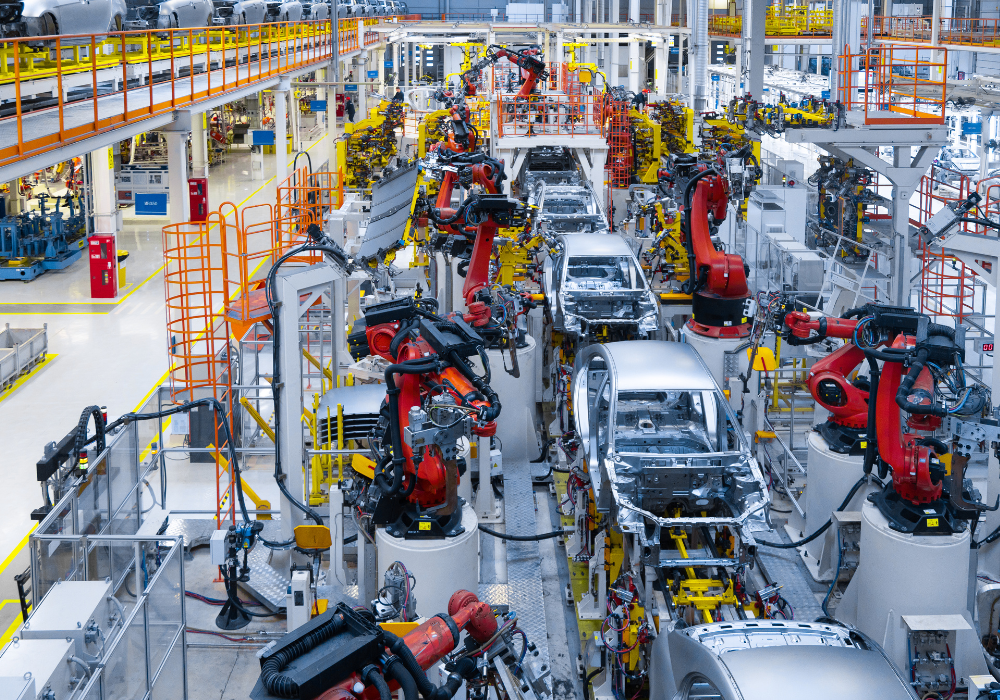
Automotive
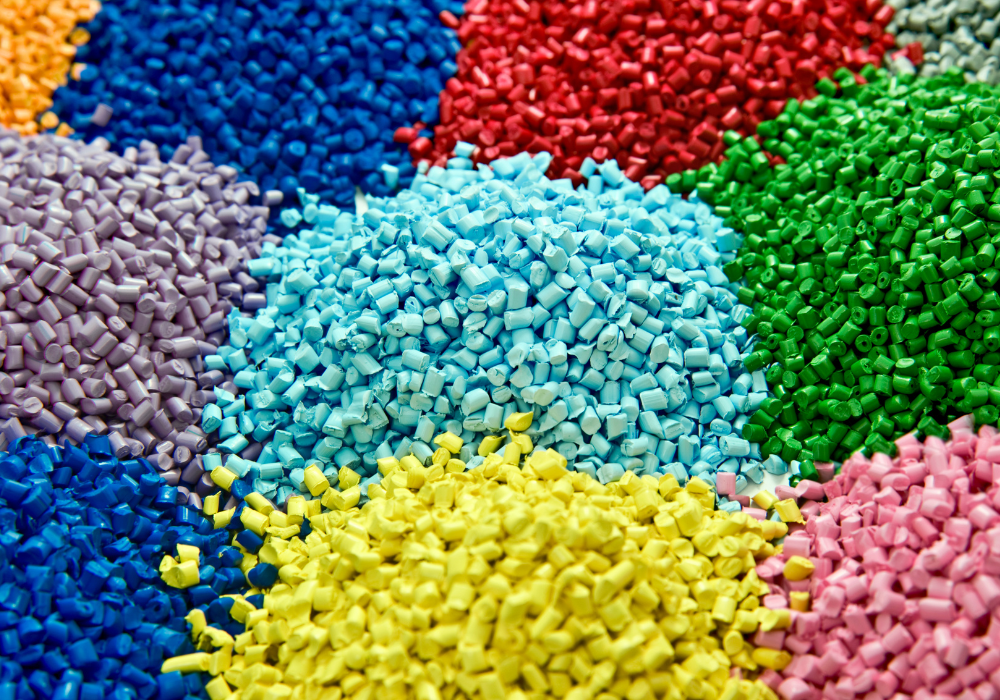
Plastics
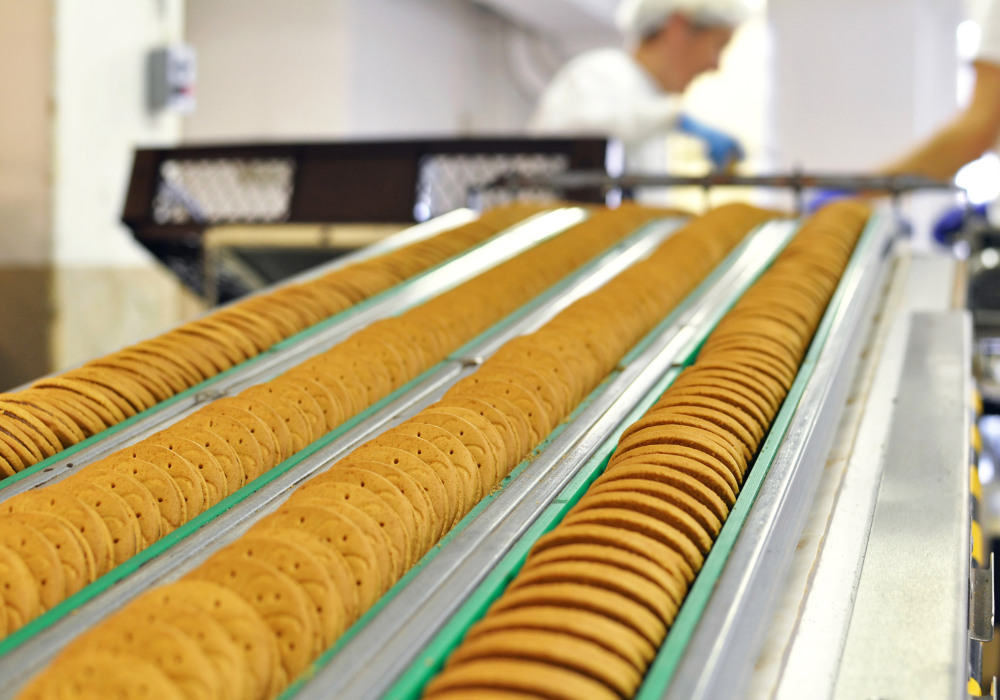
Food & Beverage
Understanding the Challenges

More than anyone else, we deeply understand the critical challenges manufacturers in Vietnam face in managing their production operations.
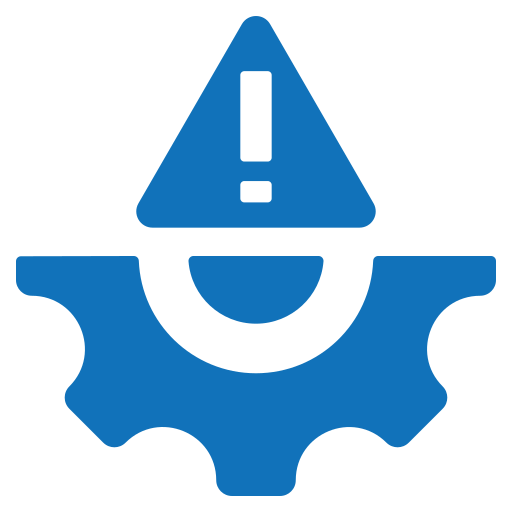
INACCURATE BOM SETUP
Lack of precise data makes Bill of Materials (BOM) creation difficult and error-prone. Often, it relies heavily on experienced personnel because data is neither properly recorded nor transparently shared.

DIFFICULT INFORMATION TRACEABILITY
Manual quality control makes it hard to trace information when product issues occur, making it unclear at which production stage problems arise.
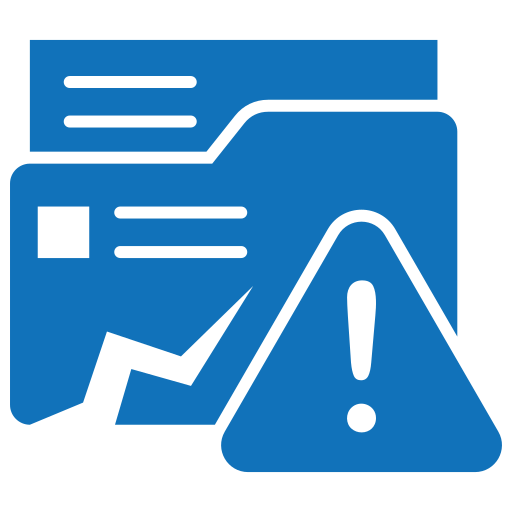
INACCURATE PRODUCTION PLANNING
Without accurate or timely data on production, inventory, and demand, production planning becomes difficult and prone to deviations.

SOFTWARE INCOMPATIBILITY
Existing software is not aligned with the plant’s actual production processes, forcing businesses to only partially utilize it, while the rest is still managed manually across various tools.
Operate Your Factory Efficiently with 4 Core Modules

Run and manage your factory production effectively and cost-efficiently with just one software: DEHA:MES. Its 4 core management modules empower you to handle all tasks necessary for an optimized manufacturing process.

PRODUCTION MANAGEMENT
- Optimize and auto-schedule production.
- Manage daily production plans with Gantt charts.
- Monitor real-time production data to detect issues early.
- Manage end-to-end production processes.
- Make production decisions more easily and accurately.
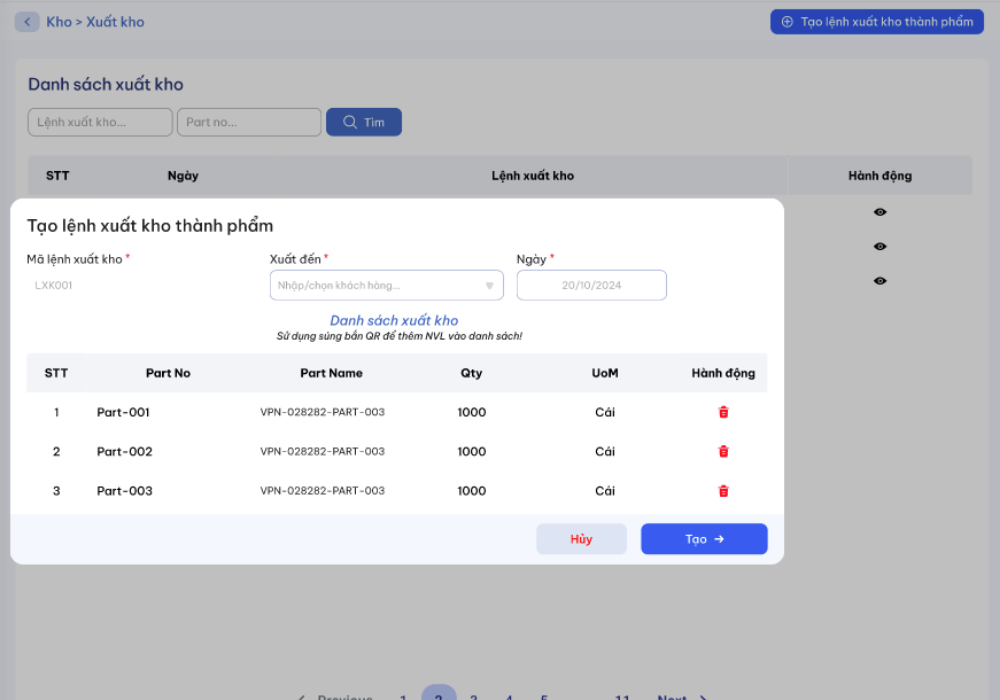
WAREHOUSE MANAGEMENT
- Automate warehouse inbound/outbound and precisely manage material locations using QR codes.
- Allocate specific storage locations for each type of product or material based on criteria such as category, batch number, production date, and size.
- Automatically calculate inventory parameters, including stock valuation.
- Set alerts and get purchase recommendations, or suggestions for products to push sales.
- Automatically calculate warehouse data to support production planning and inventory costing.
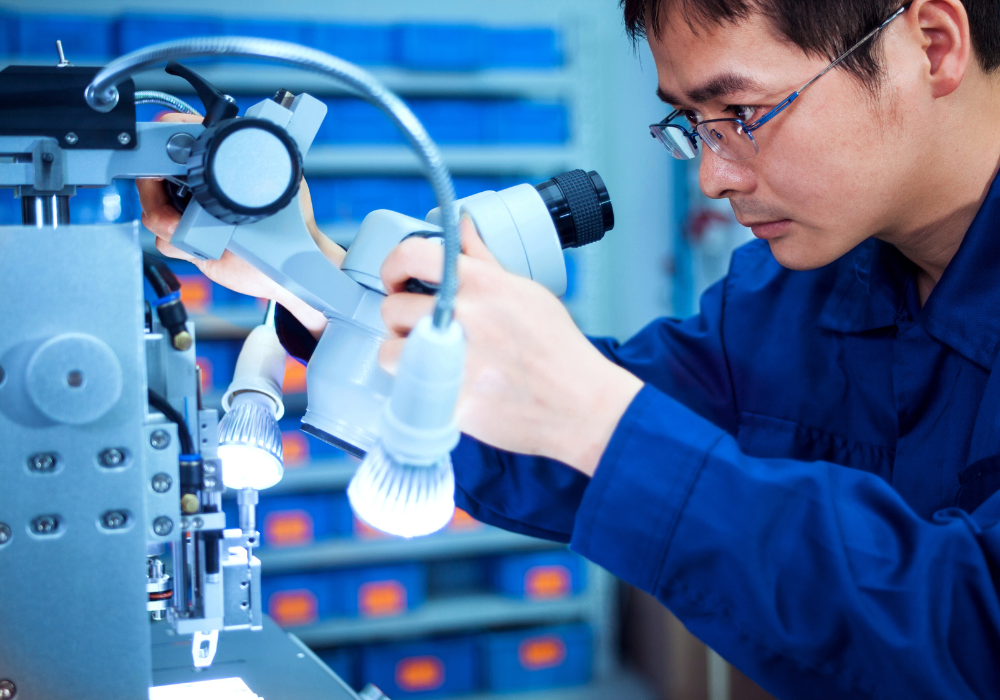
QUALITY MANAGEMENT
- End-to-end quality control from inbound to outbound (IQC – PQC – OQC).
- Record inspection results and determine product quality status (pass/fail).
- Classify defects or issues by severity level, and document detailed information for analysis and resolution.
- Alert on quality issues or non-conforming products and notify relevant stakeholders.
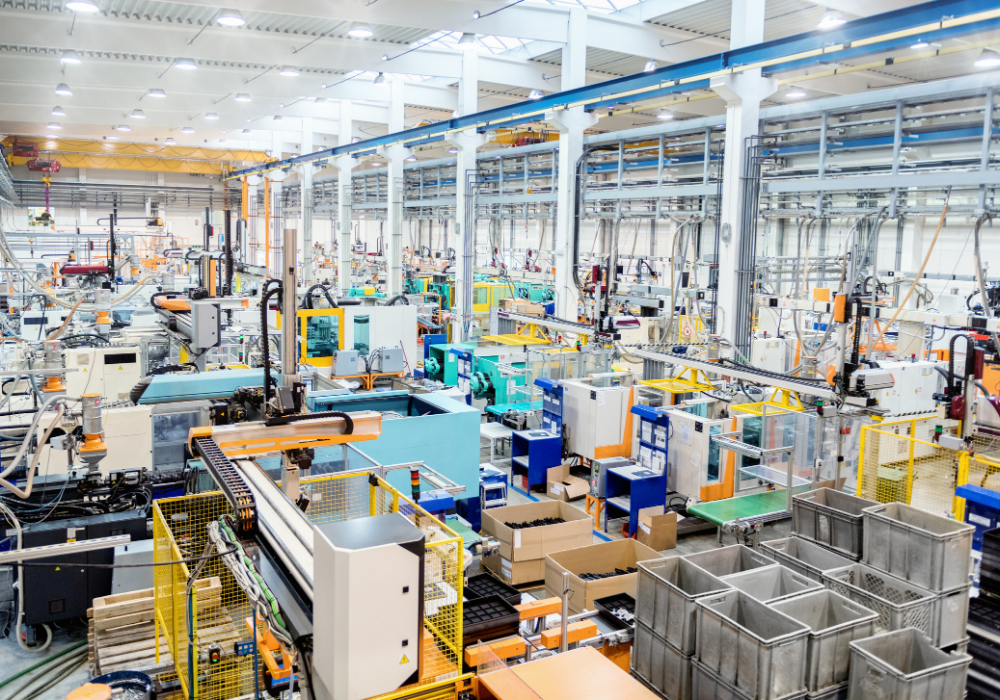
Overall Equipment Effectiveness (OEE)
- Monitor, collect, analyze, and evaluate equipment performance metrics through the IIoT system.
- Track machine and equipment downtime, log reasons for stops, and generate statistics based on this data.
- Consolidate production productivity data by shift, monitor production progress by shift, and display it on the factory floor.
Efficiently manage
your shop floor with DEHA:MES

Explore the demo of the MES system designed by DEHA Digital Solutions for an electronic components manufacturing client in Ha Nam.
Standardize Processes - Exceed Productivity

Implementing DEHA:MES brings practical benefits to your manufacturing operations, helping to improve:
+75%
Production productivity
+25%
Product quality
-35%
Operating costs
-85%
Waste reduction
Discover Real Digital Transformation Stories
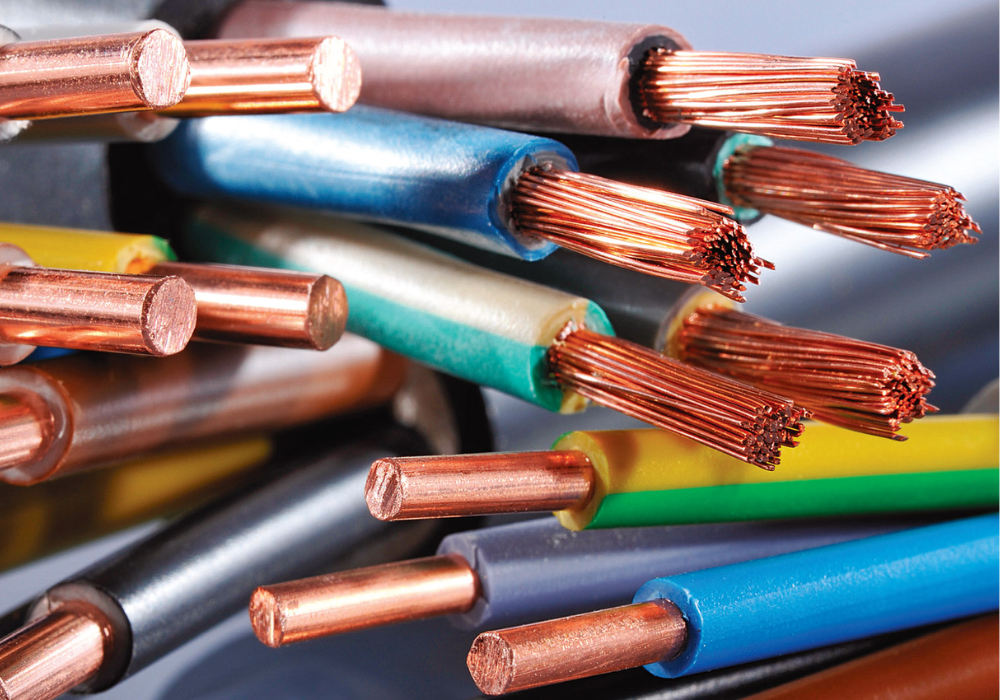
Cable Manufacturing Plant
The electrical cable manufacturing plant at Dong Van II Industrial Park implemented an MES system to manage production, addressing quality control challenges and ensuring information transparency.
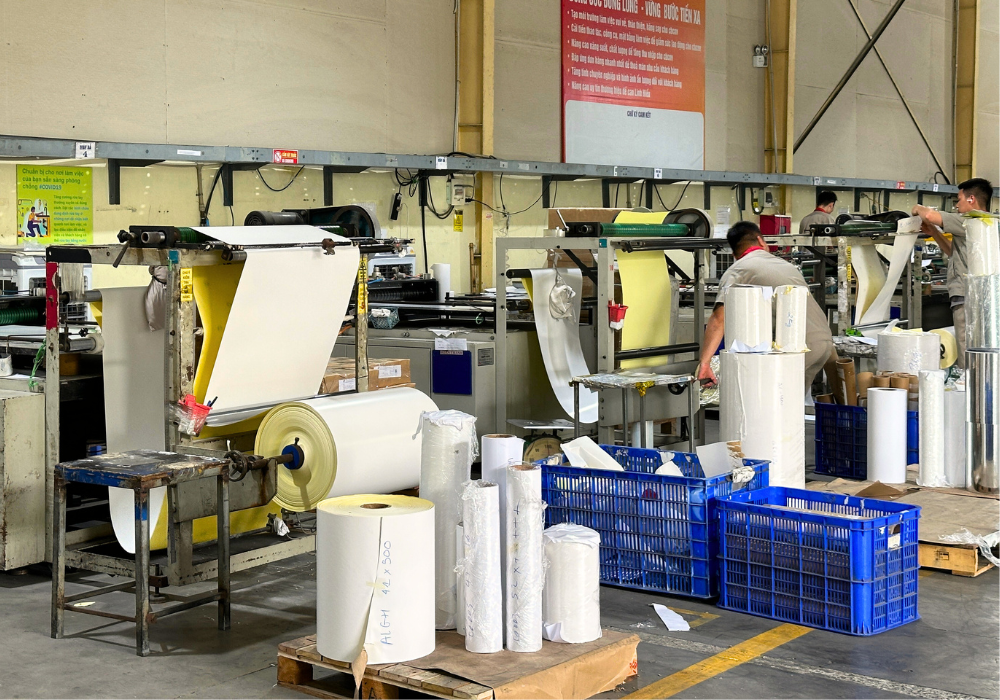
Decal Manufacturing Plant
At An Khanh Industrial Park, this decal manufacturer implemented an ERP management system to boost operational efficiency and move toward building a smart factory.
Professional Smart Factory Digital Transformation Roadmap


Start a new project
Briefly describe your project and needs so we can provide quick support.
Experienced Digital Transformation Experts


- Digital Transformation consultant and IFS Cloud implementation specialist in Vietnam with 15 years of experience.
- He has helped Vietnamese and Japanese businesses achieve successful digital transformation, especially in manufacturing sectors such as packaging, electronic devices, and electronic components.

- Expert in implementing IFS ERP Supply Chain Planning (SCP) systems with nearly 10 years of hands-on experience.
- He specializes in consulting and analyzing manufacturing operations, supporting businesses in moving from manual management models to modern systems such as ERP, MES, and WMS.
- Holder of PSM1, PSM2, and DX certifications.

- Specialist in deploying IFS ERP Manufacturing Management Systems with close to 10 years of experience.
- Certified with prestigious IT professional credentials including PSD, PSM1, PSM2, and CMMI. Well-versed in SCADA, MES, ERP, and industrial data communication protocols.
- Skilled in applying AI, Big Data, and Cloud in IIoT environments.